Abstract
This article delves deep into the differences between two common electronic connection components, spring pins and pin headers. It conducts a detailed analysis from aspects such as structural design, electrical performance, application scenarios, manufacturing processes, and cost - effectiveness, aiming to help practitioners and relevant personnel in the electronics industry clearly understand the characteristics of both, so as to make more appropriate component selections in actual work.
I. Introduction
In the manufacturing and R & D process of electronic devices, reliable electrical connections are of utmost importance. Spring pins and pin headers, as two commonly used electronic connection components, each play a unique role. Although their functions are both to achieve circuit connections, there are obvious differences in many aspects. Understanding these differences is of great significance for optimizing the design of electronic products and improving product performance and reliability.
II. Differences in Structural Design
(I) Spring Pin Structure
Spring pins usually consist of three parts: the pin head, the pin tube, and the spring. The pin head is used to contact the target connection point, the pin tube serves to protect and support the spring, and the spring endows the pin head with certain elasticity, enabling it to expand and contract within a certain range to meet different contact requirements. This unique structural design enables spring pins to maintain stable connections in the face of environmental factors such as vibration and impact.
(II) Pin Header Structure
Pin headers are generally composed of a row of metal pins arranged at a certain pitch, and the common types include through - hole and surface - mount. Through - hole pin headers are welded and fixed by inserting the pin feet into the holes of the circuit board; surface - mount pin headers are directly mounted on the surface of the circuit board and connected through the reflow soldering process. The pin feet of pin headers are relatively fixed and do not have the expandability and contractility of spring pins.
III. Differences in Electrical Performance
(I) Electrical Performance of Spring Pins
Due to their elastic contact structure, spring pins can provide a low contact resistance, ensuring good electrical conductivity. Spring pins also perform excellently in high - frequency signal transmission, being able to effectively reduce signal attenuation and interference, and are suitable for application scenarios of high - speed data transmission. In addition, the elastic contact of spring pins can, to a certain extent, compensate for contact problems caused by manufacturing tolerances or thermal expansion and contraction.
(II) Electrical Performance of Pin Headers
The electrical performance of pin headers is relatively stable, but the contact resistance is usually slightly higher than that of spring pins. In low - frequency signal transmission, pin headers can meet the needs of most applications; however, in high - frequency signal transmission, due to their fixed pin - foot structure, signal attenuation and interference are relatively large. Therefore, pin headers are more suitable for low - frequency circuit connections with low requirements for signal transmission speed.
IV. Differences in Application Scenarios
(I) Application Scenarios of Spring Pins
Spring pins, due to their good elasticity and electrical performance, are widely used in small portable electronic devices such as smartphones, tablets, and wearable devices. In these devices, spring pins are often used in parts such as battery connections, camera module connections, and antenna connections, and can achieve reliable electrical connections in a limited space. In addition, in some connection scenarios that require frequent plugging and unplugging, such as test fixtures and charging interfaces, spring pins can also give full play to their advantages and extend the service life of connection components.
Pin headers are mainly used for the connection between circuit boards, such as the connection between a computer motherboard and expansion cards, and the connection between an industrial control board and sensors. In these application scenarios, the fixed pin - foot structure of pin headers can provide a stable mechanical connection, ensuring reliable electrical connections between circuit boards. At the same time, due to the relatively low cost of pin headers, they have certain advantages in large - scale production applications that are sensitive to cost.
V. Differences in Manufacturing Processes
(I) Spring Pin Manufacturing Process
The manufacturing process of spring pins is relatively complex and requires high - precision processing equipment and strict quality control. First, the manufacturing of the pin head and the pin tube requires precise metal processing technology to ensure their dimensional accuracy and surface quality; second, the manufacturing of the spring requires special spring - forming equipment to ensure the elasticity and stability of the spring; finally, the assembly of the pin head, the pin tube, and the spring also requires a fine assembly process to ensure the fitting accuracy between various components.
(II) Pin Header Manufacturing Process
The manufacturing process of pin headers is relatively simple. The metal pin feet are mainly manufactured through stamping or injection - molding processes, and then the pin feet are arranged at a certain pitch and fixed on the plastic base. For through - hole pin headers, subsequent pin - foot cutting and shaping processes are also required; for surface - mount pin headers, special treatment is required on the surface of the pin feet to improve their solderability.
VI. Differences in Cost - Effectiveness
(I) Cost - Effectiveness of Spring Pins
Due to the complex manufacturing process and high raw material costs of spring pins, their unit price is relatively high. However, in some application scenarios with extremely high requirements for electrical performance and connection reliability, the high - performance of spring pins can effectively reduce product failures and maintenance costs caused by connection problems. In the long run, they have high cost - effectiveness.
The manufacturing process of pin headers is simple, and the raw material costs are low, so their unit price is relatively low. In large - scale production applications that are sensitive to cost, pin headers can effectively reduce production costs and improve the market competitiveness of products. However, in some application scenarios with high requirements for electrical performance, pin headers may not be able to meet the needs, resulting in a decline in product performance and indirectly increasing costs.
VII. Conclusion
As two common electronic connection components, spring pins and pin headers have obvious differences in structural design, electrical performance, application scenarios, manufacturing processes, and cost - effectiveness. In practical applications, appropriate connection components should be comprehensively considered and selected according to specific design requirements, electrical performance requirements, application scenarios, and cost budgets. Only in this way can the optimization of costs and the maximization of benefits be achieved while ensuring the performance and reliability of electronic products.
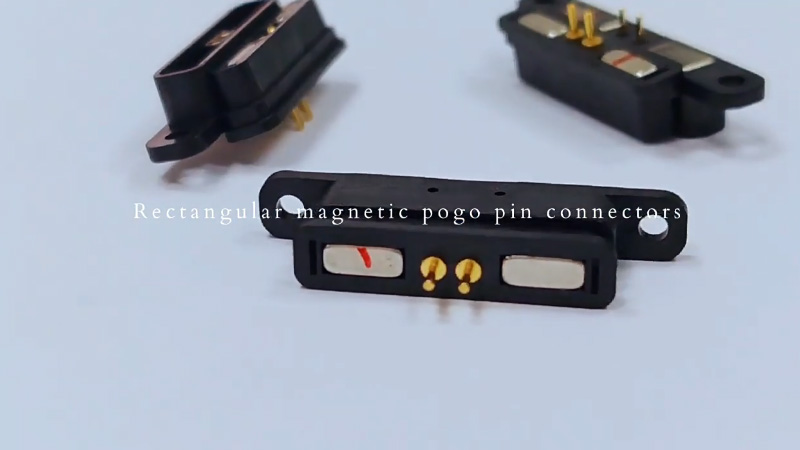